Case Studies
Our engineers re-invent automated fastening, making the improbable possible. Everyday.
Visumatic stands ready to be your fastening partner. From product evaluation to component suitability tips, we deliver improved assembly with fastening technology that spans basic operator-driven stations to full lights-out assembly. Find out below how Visumatic has guided customers just like you through all points between.
Handheld Screwdriving System Helps a Hamper Manufacturer Double Production
A long time Visumatic customer manufacturing laundry hampers has been experiencing sustained sales growth. Production was given the task of nearly doubling production of this product at their facility. The application is to drive two #6 flat head screws into a metal lid hinge.
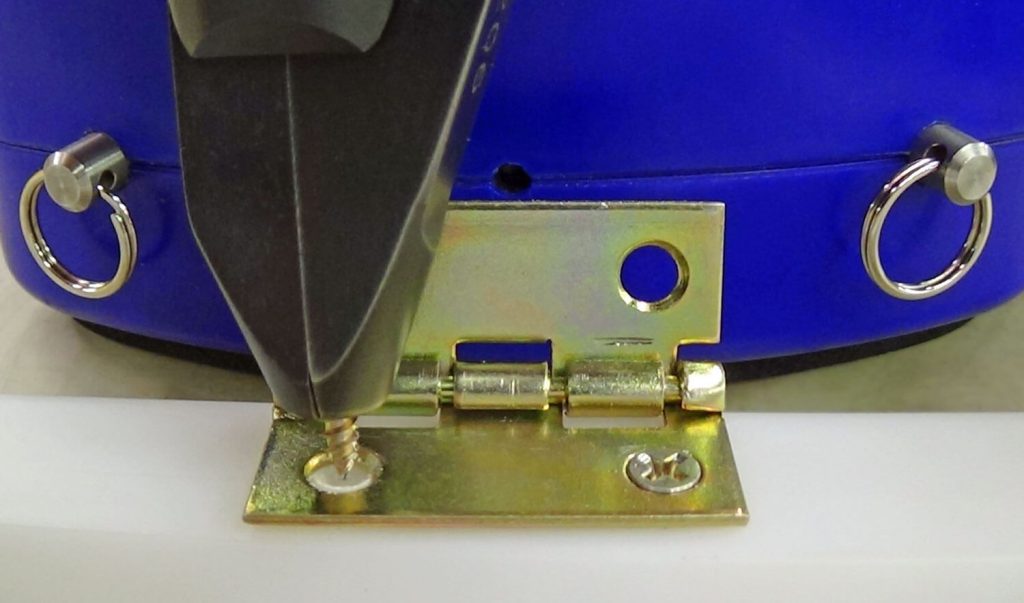
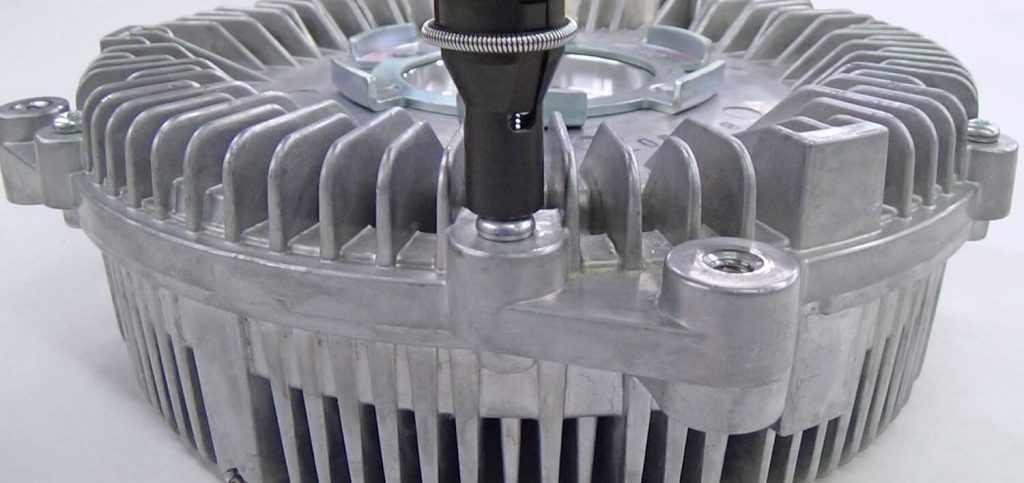
Application Spotlight – Higher Torque Screws Installed in Tight Spots
Assembly Process: Automatically feed and drive, one per cycle, an M4 x 20mm long torx drive pan head screw to required 4.8 Nm torque to secure a fan clutch housing. A radial torque arm was required to absorb the tightening reaction forces and also assist the operator with vertical alignment.
A Robot Couldn’t Touch This
Despite the drive for all-in automation, sometimes applying just the right amount can bring excellent results. An automotive head lamp manufacturer wanted to improve cycle time and increase product quality.
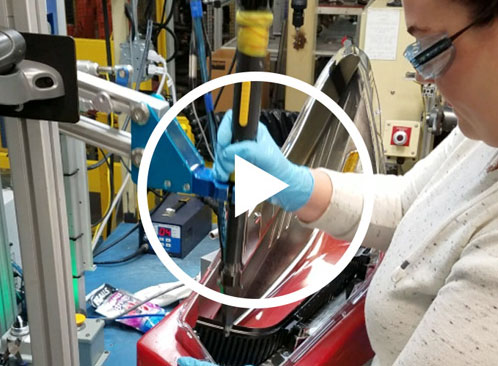
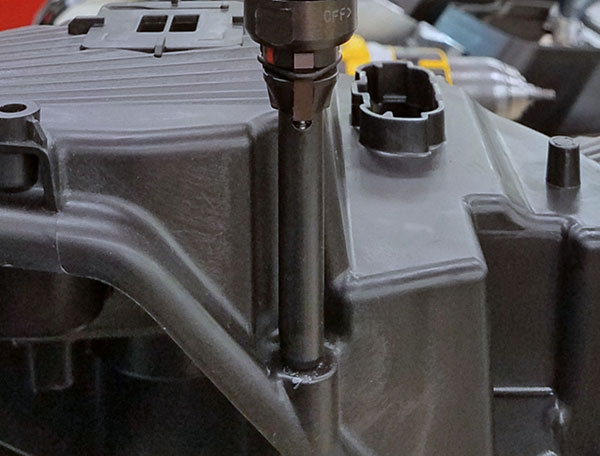
Zero Push Screw Feeding & Driving Machine Topples Tough Assembly
Tight tolerance screw driving locations and deep recess always pose challenges when hand-assembling products. An automotive manufacturer recently dealt with this during a new model release incorporating bold design changes to injection molded parts. While visually stunning, the new components were tough to assemble because of greater surface complexity and blind driving holes.
Man Against Machine ~ Taking Assembly Screwdriving to the Next Level
An automated materials handling equipment manufacturer developed a production bottle neck. The operator had to install end caps onto a series of structural extrusions, and then secure each with four (4) screws. Due to the popularity of this product, production was having a tough time meeting demand.
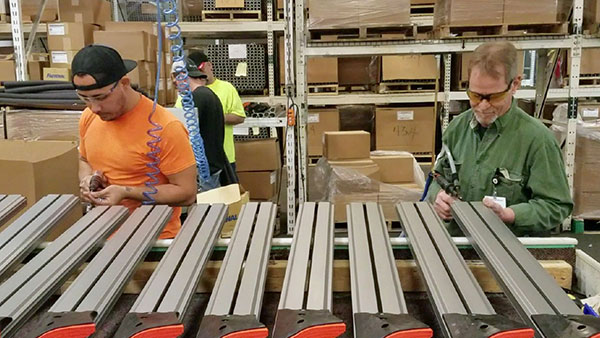
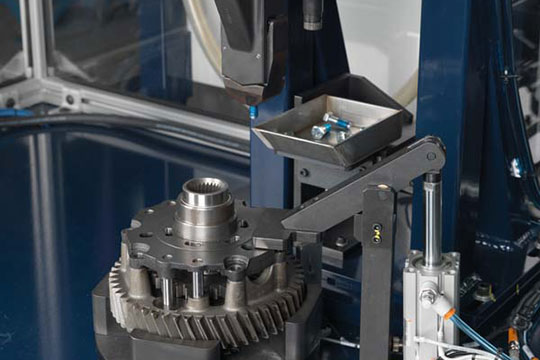
Stand Alone Bolt Driving Machine Eliminates the Strain of Manual Assembly
A casting and machine part gear box manufacturer was using an operator to perform a manual bolt placement and tightening operation with inconsistent results. Now a heavy-duty Visumatic VPD Power Driver has been applied to take on the strain of this high torque application.
Tabletop Screwdriving Machine Instantly Doubles Production
A fluid control manufacturer was faced with the challenge of increasing throughput without adding labor. The valve body had two screws per part, with a multi-component stack up that included a spring. This made consistent fastening very challenging for an operator doing manual assembly.
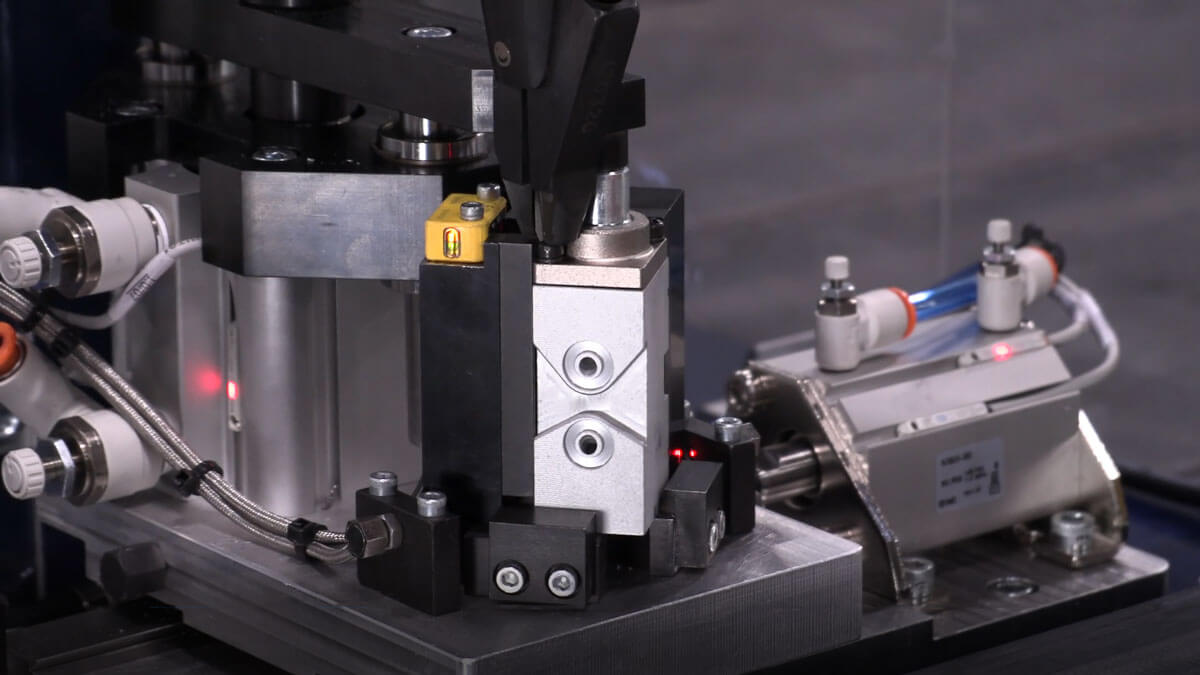
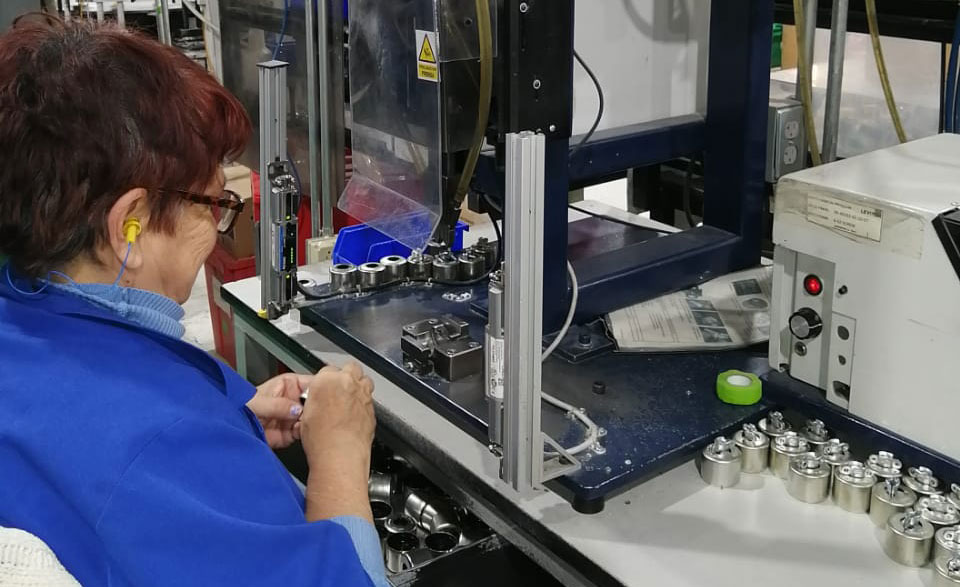
Tabletop Assembly Machine Tackles Tight On-Center Spacing
An electrical products manufacturer was struggling to maintain production numbers without adding labor. This application required two screws to be driven to depth into a metal electrical connector. Due to the customer’s workflow demands, Visumatic chose a flexible tabletop design approach, to allow for quick deployment.
Automating an “Impossible” Bolt with Oversized Captivated Washer
Visumatic delivers on automated fastening promise to a metal stamping manufacturer. Their end-user asked them to do some value-add by producing a completed assembly instead of loose parts.
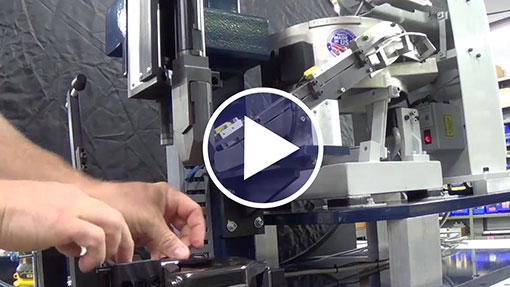
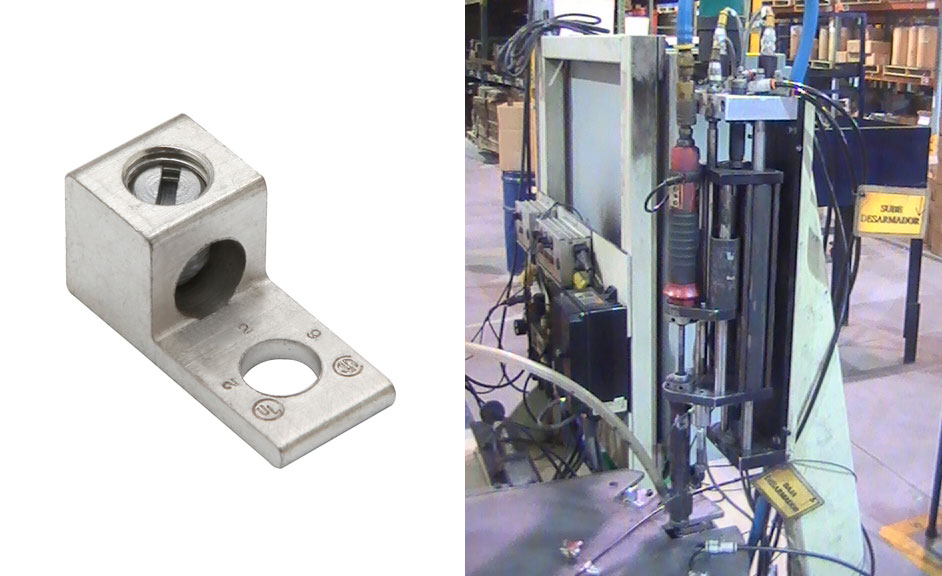
Never-Stop Assembly Machine Hits 20-Year Production Mark
An electrical lug manufacturer came to Visumatic in 1999 looking to reduce labor and radically improve throughput for a mature product. A rotary indexing system was created, combining a single VPD Power Driver and a set of Model 94 feeders.
Bolt Driving System Provides Capability for Rapid Automation Deployment
A beam clamp manufacturer began the process of fully automating their assembly process. They approached Visumatic to provide the feed and drive componentry for their machine build group.
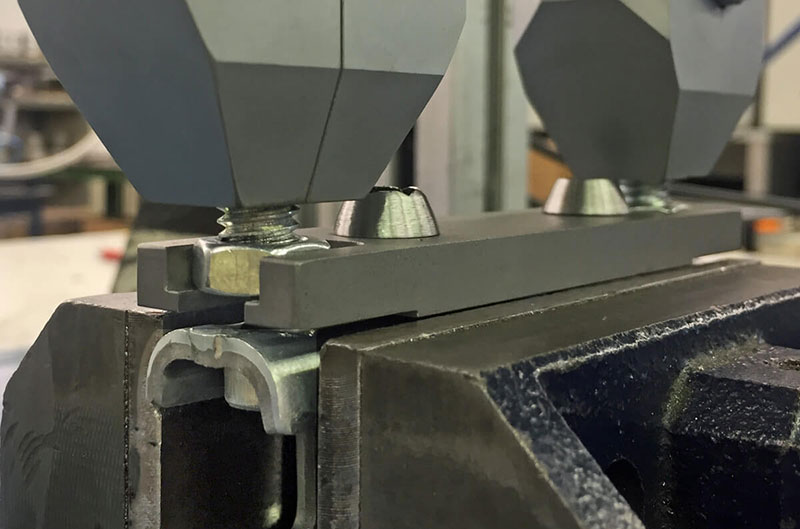
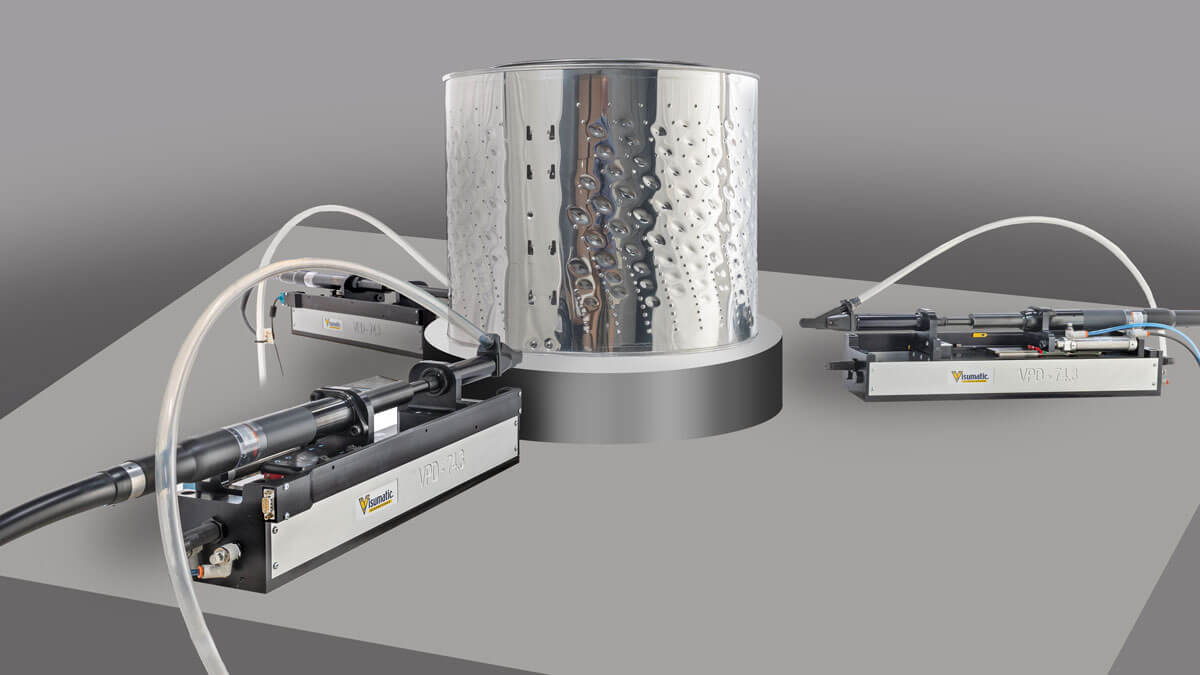
White Goods Manufacturer Smashes Productivity Barriers
An appliance manufacturer’s in-house build group was looking to clear the bottle neck on their washing machine assembly line.
Smooth Robot Integration and Solid Performance Reported by Integrator
A machine builder was working on a very challenging assembly project for an aerospace component assembly application. They began searching for a fastening solution to accurately and repeatably drive screws inside of their robot cell.
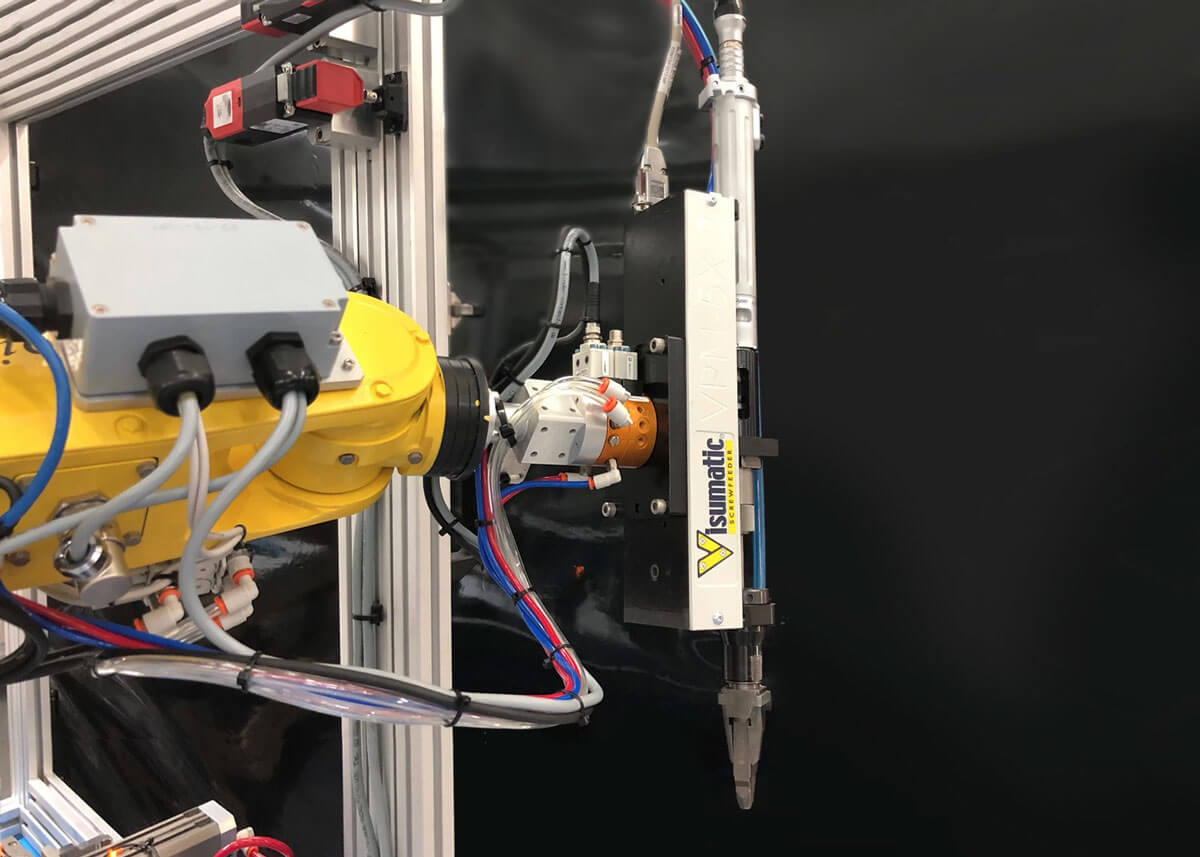
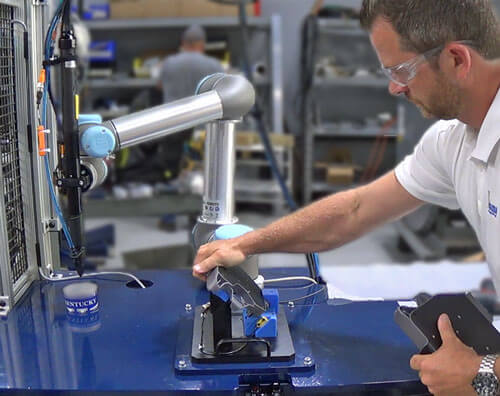
Cobot Workstation Jump Starts New Product Production
An electronics manufacturer was rolling out an updated product design and they wanted to prove out a new form of process automation at the same time.
Automation Group Nails Proof of Concept with Cobot Screwdriver Assist
An appliance manufacturer purchased a handheld automatic screwdriver to speed up production on a fan assembly. Their in-house machine build group began exploring the idea of taking automation to the next level using collaborative robots for this application, as well as the next targeted high-volume product.
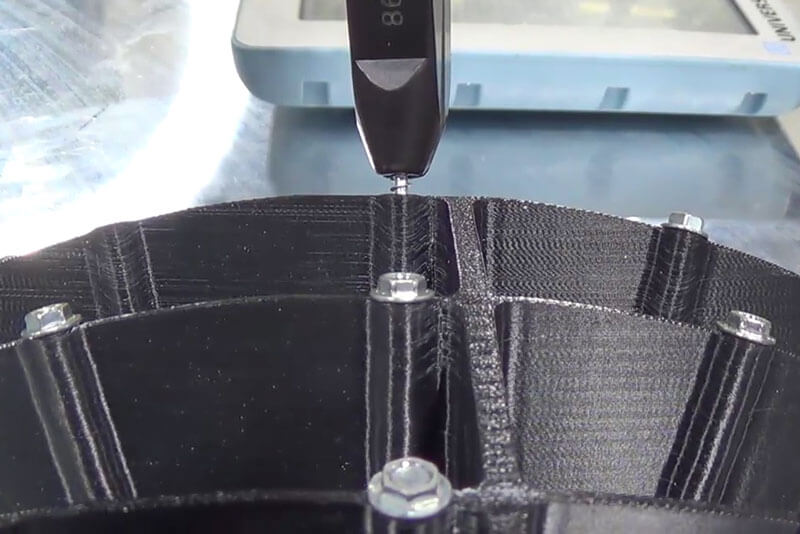
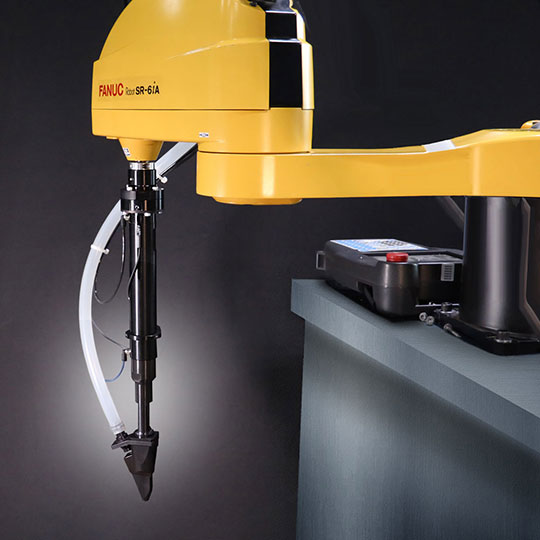
Screwdriving Robot Delivers Speed and Streamlined Integration
An automotive air intake manufacturer reached out for assistance assembling a new model with multiple screws joining case halves with a sealing gasket in between.
Multiple Robots Deliver Iron-Clad Quality Control without Raising Headcount
A Tier 1 automotive interior trim manufacturer was tooling up for a new model year. The final assembly plant wanted the parts delivered in sets as they were to be vehicle installed on the line.
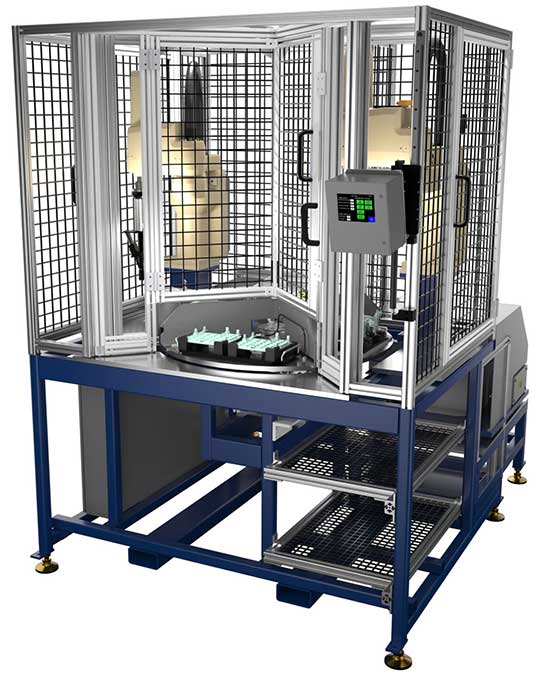
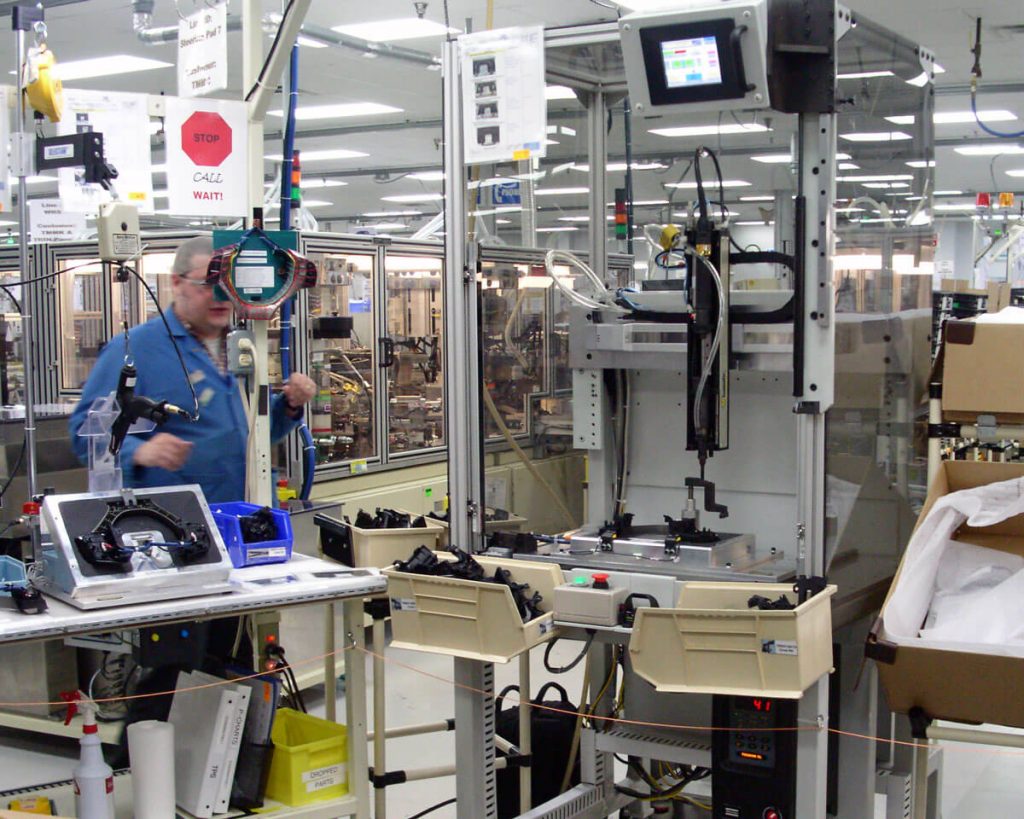
Essential Automation Engineered to be Made Simply
An automotive steering wheel manufacturer was looking for labor savings to boost their competitive advantage for a switch assembly process. The end customer increased quality assurance requirements without providing capital equipment funding. Visumatic teamed up with the factory process engineers to create a cost-effective solution.
Robot Screwdriver & Clip Inserter Machine Provides Next-Level Quality Control
Along with a mid-model design change, this automotive interior trim maker saw their production target triple. Already struggling with some quality concerns, they met with Visumatic to review the assembly process and explore options.
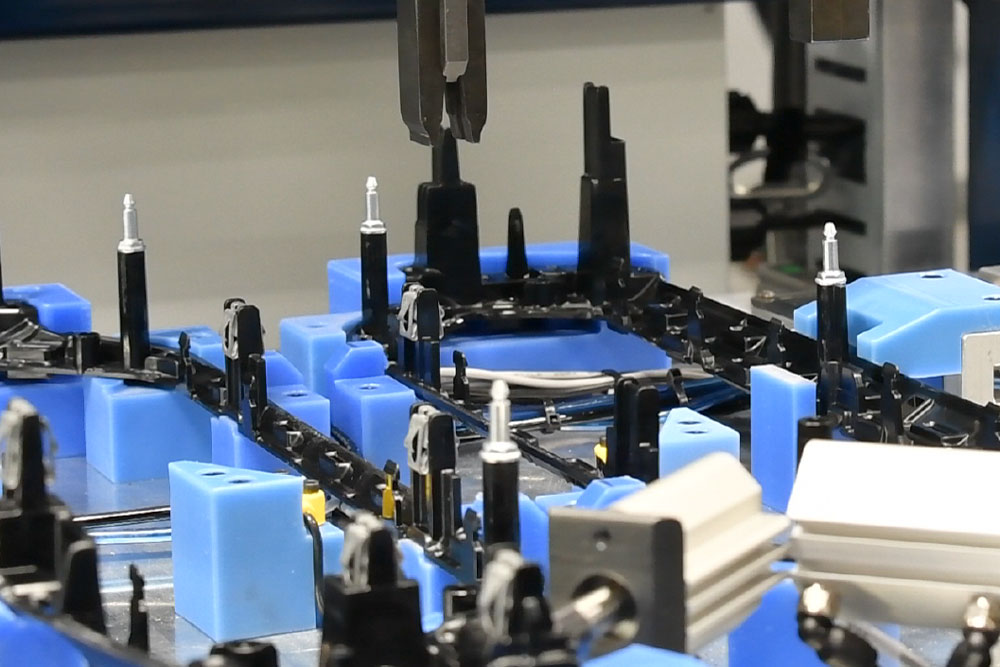
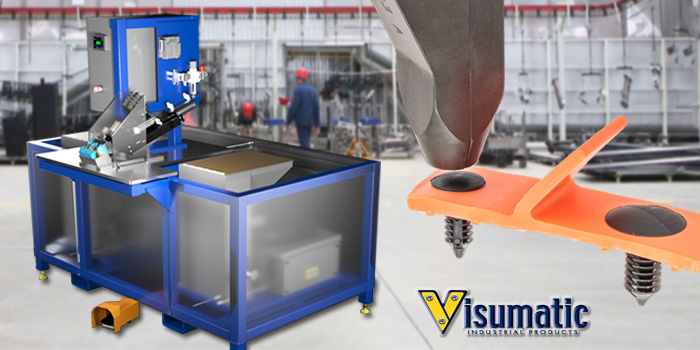
Pin Insertion Gear Makes Difficult Assembly a Breeze
An injection molding company began a value-add for their automotive manufacturing customer. Operators were strained ergonomically handling and pushing the pins through the material and quality was suffering. With a high defect rate and a dramatic increase in production volumes, their manufacturing engineers reached out to Visumatic for options.
Automatic Screwdriver Brings Ergonomic Relief to Joining Operation
Faced with the need to increase throughput on already strained operators, an office chair manufacturer turned to Visumatic to jump start productivity. The stamped metal components required manual manipulation to align with the mating seat base, so full automation was immediately out of consideration. With the operators under stress, something had to be done.
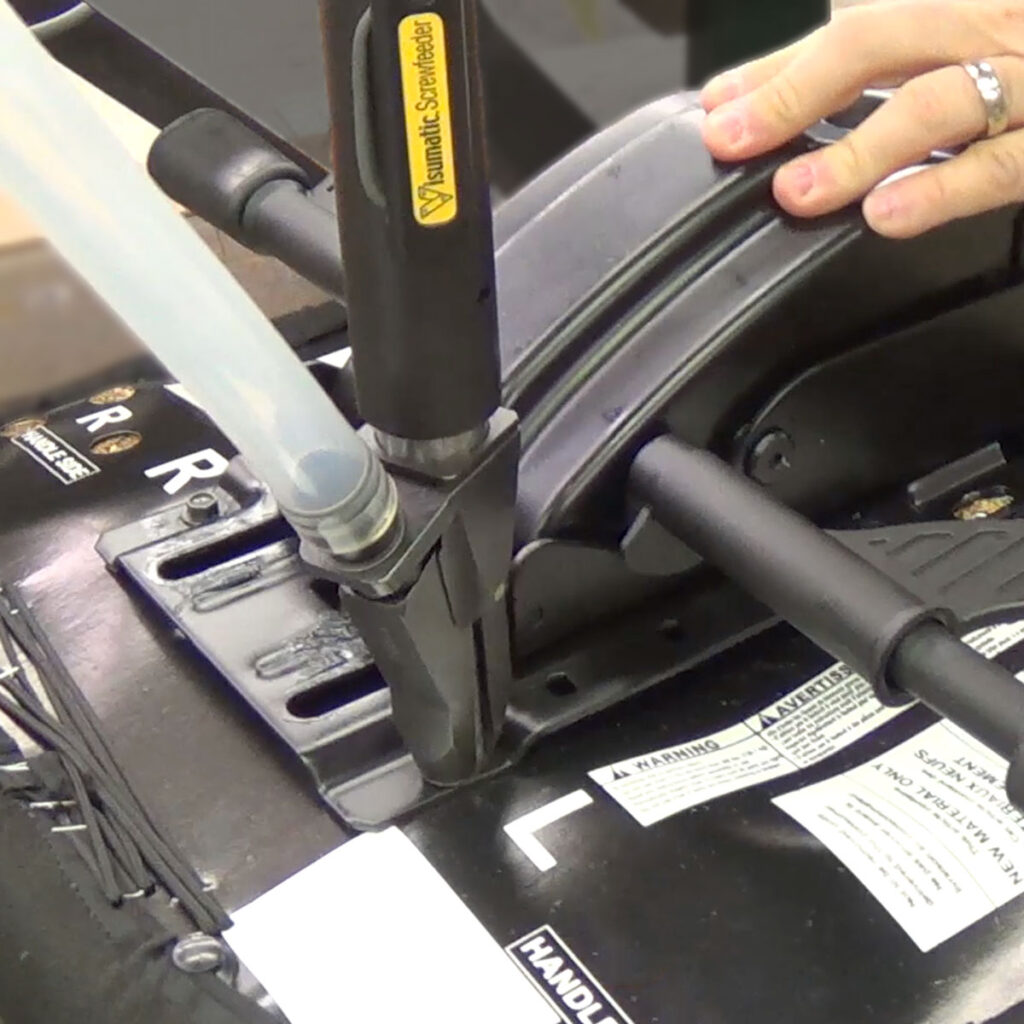